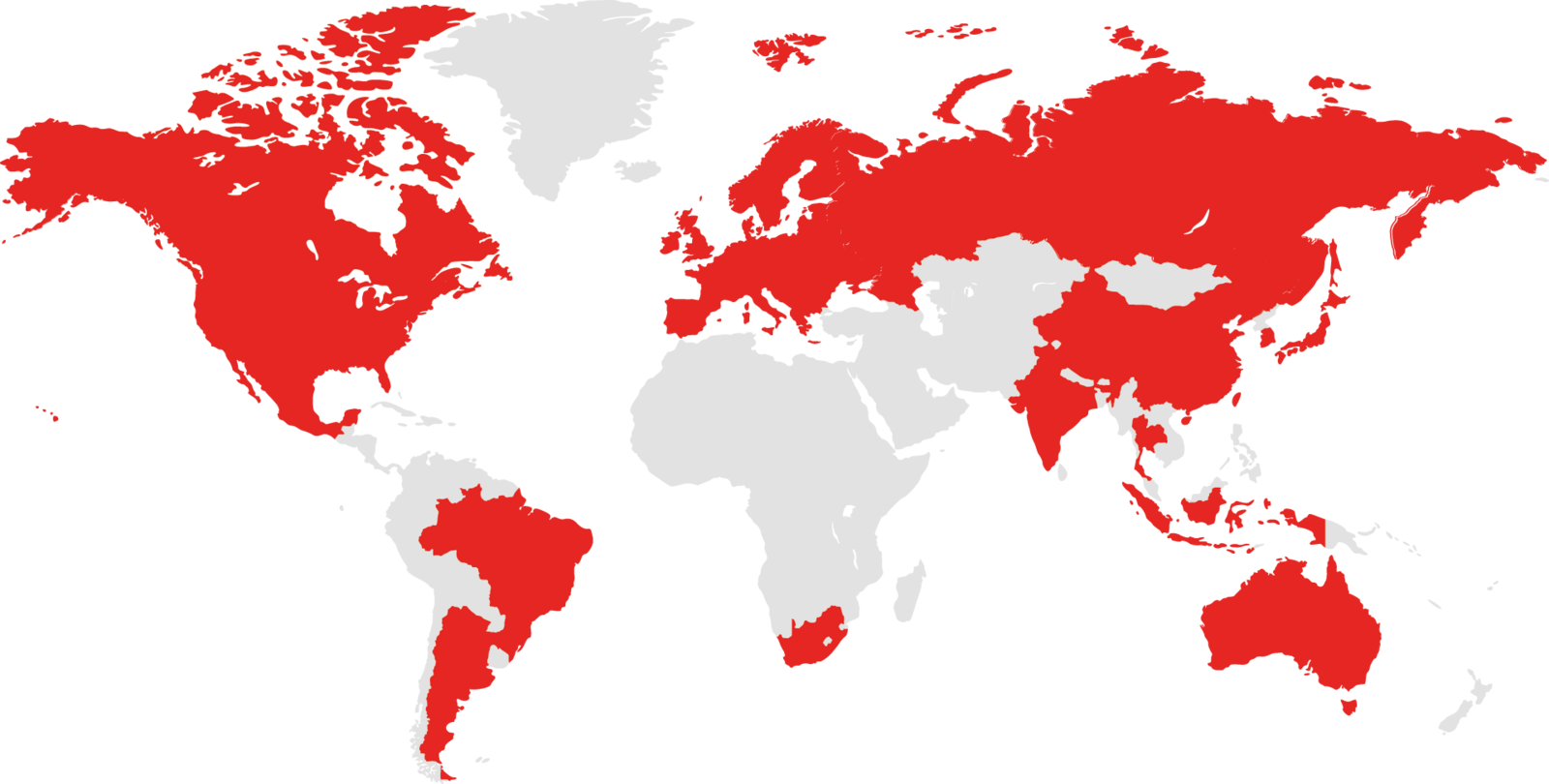
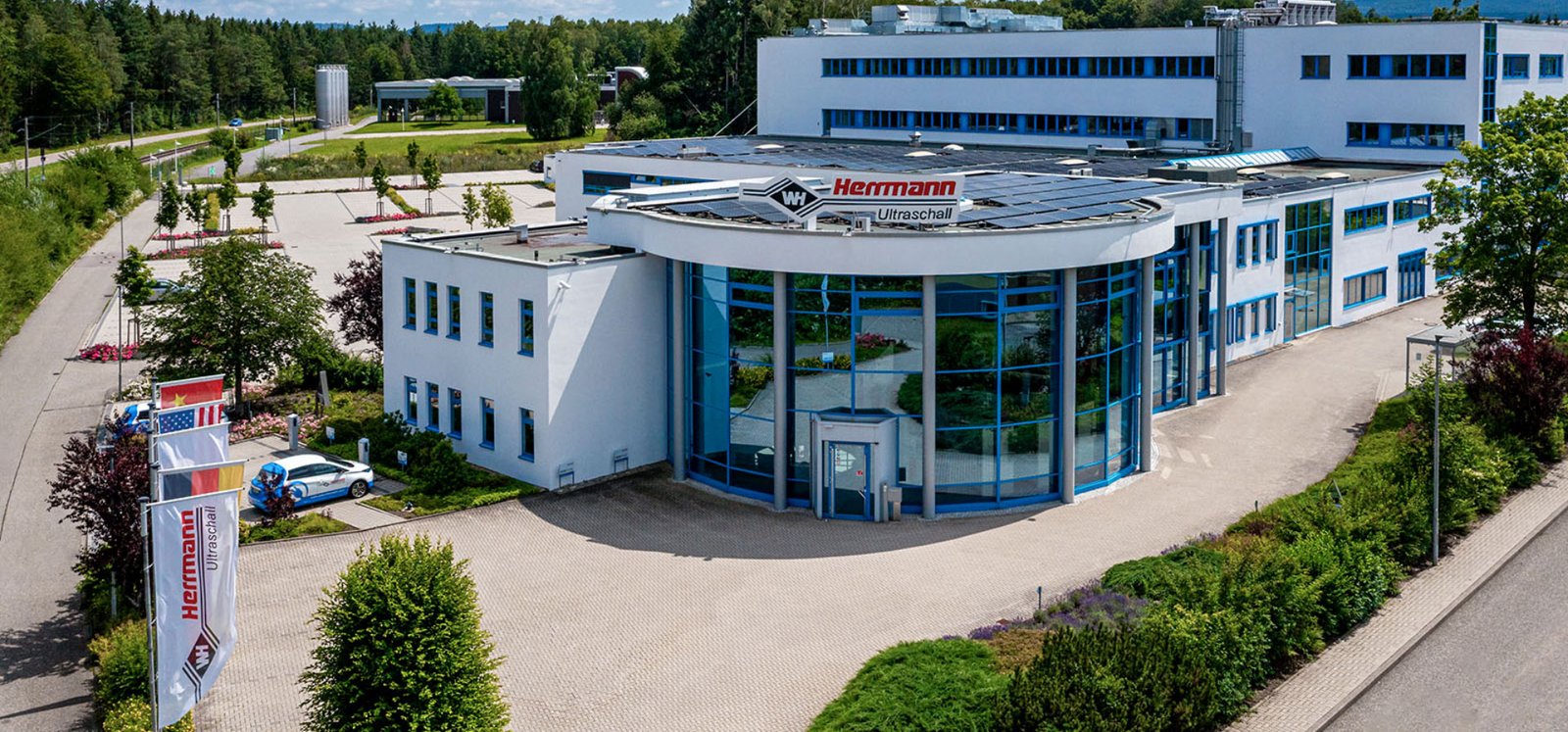
Bonding - more than materials
Who we are and what makes us different
Think globally, act locally!
Operating worldwide with partners
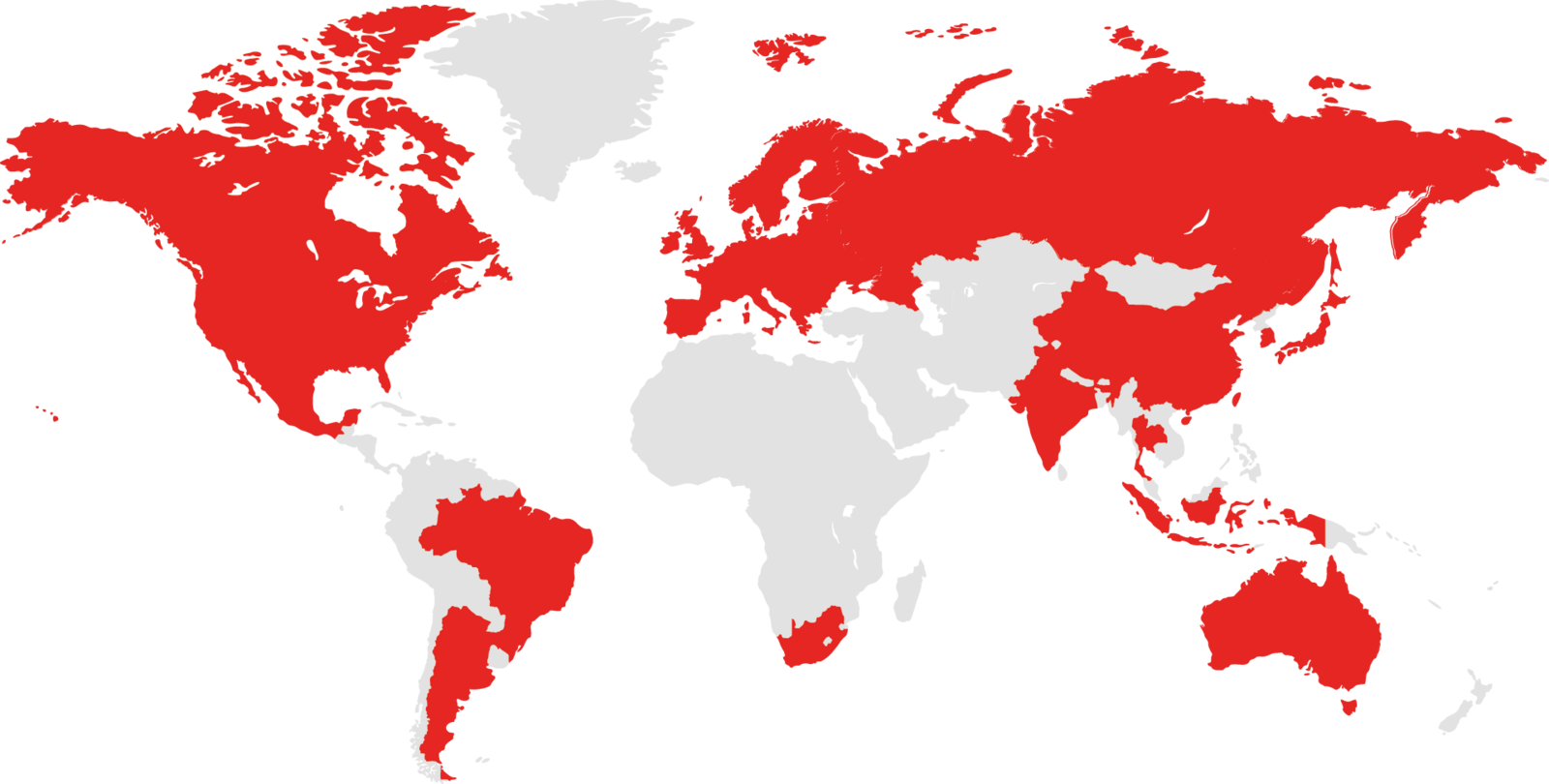
PACKAGING History
Who we are and what makes us different.
Bonding more than materials
We see ourselves as your technology partner and solution specialist. Our aim is to increase the economic efficiency and quality of your application – for sustainable and environmentally friendly processes.
We work with you to develop customized solutions which correspond to your demands precisely. As experts in our field, we develop applications which make your project a success. Here, we rely on long-standing technology partnerships and the results from over 40 high-tech laboratories around the world.
We offer a premium product portfolio with the highest quality standards – made in Germany. We stand for top weld results, professional integration and durability of all ultrasonic components and modules for an economical overall solution.
We guarantee reliability, safety and a quick on-site service as part of our concept, and immediate support in over 20 countries. For you, this means quick help when you really need it – at any time and in your local language.
A simple route to more sustainability: not a problem with our efficient ultrasonic technology! The ability to do without joining materials and the low energy consumption mean that your production process will automatically become more sustainable. Reliable bonding will also reduce your rejects and prevent you from generating unnecessary waste.
Leverage our expertise and optimize your packaging process!
Contact us and we will launch a project together that will enable you to incorporate the sustainability megatrend into your company – conveniently, quickly, and cost-effectively.